Rubber roof repairs are essential to prevent water intrusion, safeguard building assets, and extend the lifespan of your roof. In Canal Fulton, many industrial properties depend on durable rubber roofing systems like EPDM for their longevity and minimal upkeep. However, even the toughest roofs can suffer from wear, seam separations, or punctures over time. These minor issues can escalate into major leaks if left untreated and cause costly damage.
Miller’s Commercial Roofing specializes in expert rubber roof repairs designed to address these problems before they worsen. With decades of experience as commercial roof repair contractors, we identify problem areas accurately and apply lasting, watertight solutions. In this blog, we’ll show you how regular maintenance and timely repairs can extend the life of your roof and reduce your overall maintenance costs.
The Role of Rubber Roofing in Industrial Facilities
Rubber roofing is used in industrial buildings because it’s affordable, easy to install, and resists weathering. EPDM (ethylene propylene diene monomer) is one of the most common rubber materials for commercial roofs. It works well on flat or low-slope buildings, especially in warehouses, factories, and office complexes.
Rubber membranes come in large sheets. Therefore, there are fewer seams and less chance of leaks. For facility managers, rubber roofing offers a cost-effective way to cover large roof areas. It also stands up to regular foot traffic, rooftop equipment, and most chemical exposures.
Why Rubber Is Common in Flat Roof Systems
Rubber roofs are common on flat systems because they create a smooth surface that drains water efficiently. Flat roofs don’t shed water like pitched roofs, so materials must resist standing water. EPDM handles this by staying flexible and sealing tightly at seams, flashing, and penetrations. It’s also compatible with various roof coatings and insulation systems, making it easy to modify or upgrade over time.
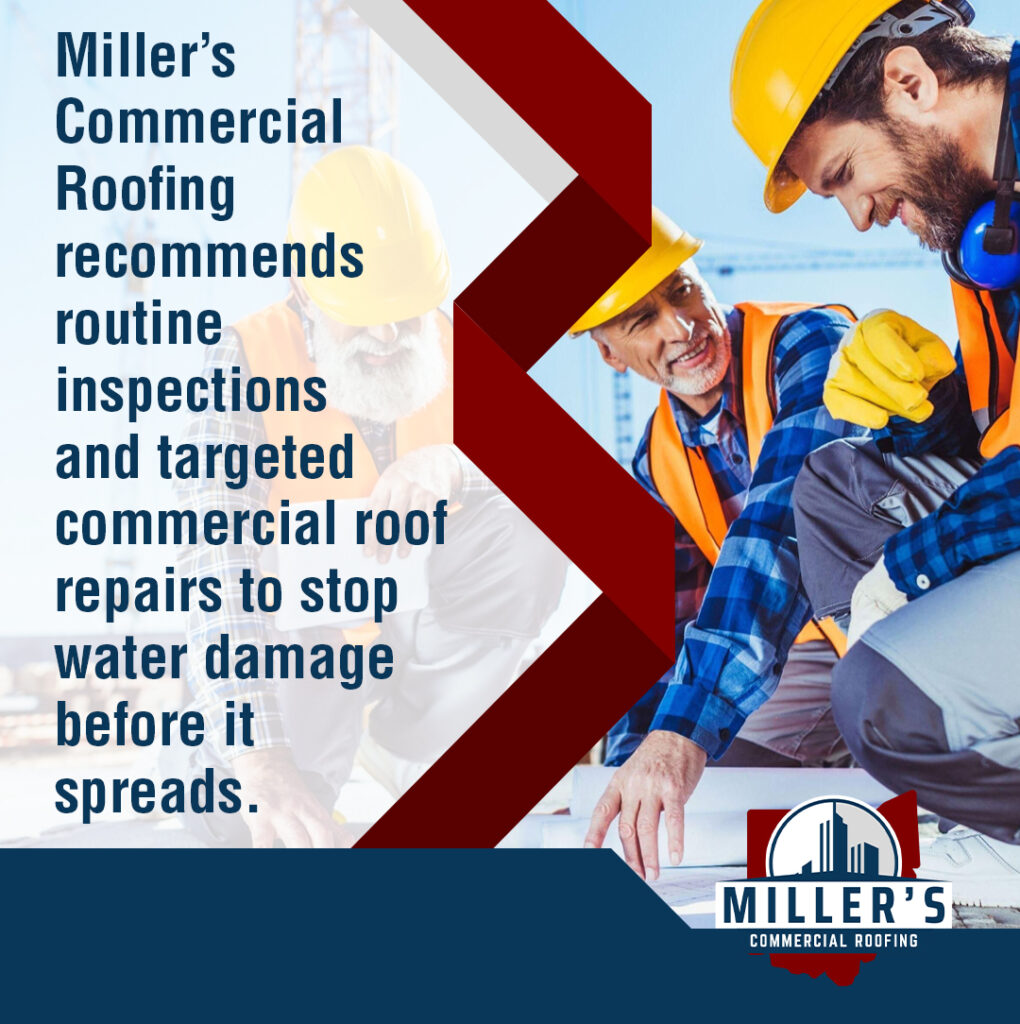
How EPDM Performs in Ohio’s Weather Conditions
EPDM holds up well in Ohio’s freeze-thaw cycles, high humidity, and heavy summer rains. Rubber roofs expand and contract without cracking, which is important in climates with large temperature swings. EPDM resists UV damage during hot summers and remains pliable during cold snaps. It also doesn’t get brittle, which prevents splitting over time.
This performance makes EPDM a good long-term choice for commercial roofing in Northeast Ohio, where winters can be harsh and summers bring heavy storms.
Typical Lifespan of a Rubber Roof Without Repairs
Without repairs or maintenance, a rubber roof usually lasts 10 to 15 years. Small punctures, seam separations, or drainage issues can develop earlier if the roof isn’t inspected regularly. Dirt buildup and ponding water can also wear down the membrane faster. These issues shorten the roof’s lifespan and lead to leaks that affect interior operations.
As a commercial roof repair contractor with extensive experience, we recommend routine maintenance to catch problems early. With proper care, EPDM roofs can last longer, even in demanding industrial environments.
Risks of Overlooking Minor Rubber Roof Issues
Even small roof problems can lead to major repair costs if ignored. A small tear or seam separation in a rubber roof might not seem urgent. However, water can enter the system, soak the insulation, and damage structural materials underneath. Minor issues also tend to get worse after heavy storms or freeze-thaw cycles. For commercial buildings in Canal Fulton, early detection of roof damage can help avoid interior repairs, tenant complaints, or shutdowns due to safety issues.
How Small Leaks Create Larger Structural Problems
Water from small leaks can spread across insulation and decking, weakening the roof from the inside. Because rubber membranes cover large, flat areas, even a small puncture can let in enough water to reach distant parts of the roof. The water may pool between layers, causing wood rot, corrosion, or mold growth. Once structural decking is compromised, repairs are more costly and time-consuming.
This is why at Miller’s Commercial Roofing, our commercial roof repair contractors inspect not just the membrane but also the layers below, especially after storms or snow melts.
Impact on Insulation, HVAC, and Utility Costs
Water-damaged insulation makes HVAC systems work harder, increasing energy bills. When moisture gets into the insulation beneath a rubber roof, it reduces its thermal resistance (R-value). That means buildings lose heat faster in winter and gain it faster in summer.
HVAC units have to run longer to keep up, which leads to higher utility costs. In industrial facilities with large square footage, even small drops in insulation performance can add hundreds of dollars to monthly operating costs.
Safety Hazards from Water Intrusion in Workspaces
Leaks can create slip hazards, mold exposure, and electrical risks inside the building. Water entering through a damaged rubber roof often travels before it appears. It may drip near machinery, hallways, or workstations, creating dangerous conditions for staff. Mold can also form behind walls or under floors, causing air quality issues. If water reaches electrical systems, there’s also a risk of shorts or fire.
At Miller’s Commercial Roofing, we help prevent these risks with regular inspections and fast commercial roof repair services to keep buildings safe and dry.
Commercial Roof Repairs: What Counts as “Routine”?
Routine commercial roof repairs include small fixes that stop bigger problems before they start. These include sealing minor cracks, reattaching loose flashing, resecuring edge metal, and clearing clogged drains. In Canal Fulton’s climate, these small steps can prevent costly issues caused by water buildup, ice dams, and heat expansion.
Seasonal Repair Considerations for Canal Fulton Properties
Different seasons bring different commercial roof repair needs for industries in Ohio. Spring and fall are key times to check for storm damage, membrane wear, or pooling water. Summer heat can cause seams to expand or adhesives to break down. Winter brings freeze-thaw stress, which can widen small cracks or shift flashings.
At Miller’s Commercial Roofing, we time the commercial roof repair services and inspection work around these seasonal risks to help business owners avoid downtime and surprise costs.
Cleaning and Drainage Checks
Blocked drains and debris buildup are leading causes of roof damage on flat commercial buildings. Leaves, dirt, and roofing materials can clog internal drains or scuppers. When water can’t flow off the roof, it pools, adding weight and increasing the risk of leaks. This can shorten the life of the membrane or cause structural sagging. At Miller’s Commercial Roofing, we include drainage checks and debris removal in all routine maintenance plans to keep commercial roofing systems working properly.
Flashing, Seams, and Edge Repairs
Flashing and edge details are common points of failure in commercial roofing systems. On rubber roofs, seams around skylights, vents, HVAC curbs, and parapet walls are more likely to wear out. Flashings may pull away from surfaces due to thermal movement or age. Edge metal can also loosen and let wind and water get underneath.
At Miller’s Commercial Roofing, we use long-lasting sealants and mechanical fastening methods for rubber roof repairs to restore these areas and prevent recurring leaks.
Making Repairs Part of a Larger Maintenance Strategy
Repair work should support a larger plan that protects the entire roofing system. A single patch may stop a leak, but it won’t prevent new issues without regular maintenance.
At Miller’s Commercial Roofing, we encourage business owners to tie repairs into a broader strategy. This includes tracking roof conditions over time, identifying repeat problem areas, and using data from past service calls to guide future actions. A maintenance-first approach reduces unexpected rubber roof repair costs and extends its life.
Scheduling Inspections to Catch Issues Early
Regular inspections help find small problems before they cause major damage. Minor issues like seam gaps, membrane wear, or clogged scuppers are easy to miss without a trained eye. For industrial buildings in Canal Fulton, a biannual inspection schedule—ideally in spring and fall—is recommended. As a commercial roof repair contractor, we provide detailed inspection reports so facility managers can act before issues grow.
Planning for Mid-Lifecycle Repairs
Roofs around 10–15 years old often need more than minor fixes to stay watertight. At this stage, the membrane may show surface wear, flashing might separate, and UV damage can reduce elasticity. Instead of waiting for failure, our commercial roof repair contractors help clients plan mid-cycle repairs that restore function without full replacement. These may include partial membrane overlays, seam reinforcement, or roof coatings. This approach extends the useful life of the roof by several years.
Integrating Repairs with Long-Term Budgeting
Rubber roof repairs should be planned and budgeted. Unexpected leaks and emergency fixes are often more costly than scheduled maintenance. At Miller’s Commercial Roofing, we help business owners map out their commercial roof repair needs over time. By combining inspection findings with expected wear patterns, property managers can allocate funds for repairs in advance. This keeps the roof in good shape and helps control long-term facility costs.
Timing and Weather: Factors That Affect Roof Repair Windows
Weather plays a key role in how and when rubber roof repairs can be done. Cold temperatures, high winds, or rain can delay work or affect the quality of the repair. Rubber materials like EPDM require dry surfaces and stable temperatures to bond correctly. For businesses in Canal Fulton, Ohio, scheduling commercial roof repair services during favorable weather helps long-term performance and fewer follow-up issues.
When Repairs Are Most Practical in Northeast Ohio
Spring and fall offer the best conditions for most rubber roof repairs. These seasons typically provide mild temperatures and lower rainfall. EPDM adhesives cure best between 55°F and 80°F, which matches spring and fall weather in Canal Fulton. Winter often brings too much moisture or freezing conditions, while summer heat can soften materials, although it’s usually not an issue for reputable installers.
How Temperature Affects Rubber Adhesion and Curing
Rubber adhesives need time, temperature, and dryness to set properly. In cold weather, adhesives can stiffen and fail to bond. In extreme heat, they may cure too fast, creating weak spots. These issues shorten the repair’s lifespan and may cause leaks to reappear. Commercial roof repair contractors at Miller’s Commercial Roofing adjust product choices and techniques based on the current forecast to maintain quality.
Dealing with Emergency Repairs During Storm Season
Emergency roof repairs are sometimes necessary during Ohio’s stormy months. Heavy rain or high winds can cause sudden damage, especially on aging rubber roofs. In these cases, Miller’s Commercial Roofing offers emergency response services. Our crews stabilize the area with temporary patches or covers, and when conditions improve, we complete the repairs. Quick action limits water damage and helps businesses keep operations running during harsh weather.
Working with Miller’s Commercial Roofing in Canal Fulton
Miller’s Commercial Roofing works directly with business owners to create commercial roof repair plans that match the building’s needs and budget. From the initial visit to the final inspection, our focus stays on practical solutions. This approach gives local businesses more control over maintenance decisions and long-term costs.
Site Evaluation and Honest Scope Review
Every job starts with a full roof inspection and clear reporting. Before recommending repairs, Miller’s Commercial Roofing evaluates the current condition of the roof, drainage, seams, and insulation layers. This prevents guesswork and helps identify problems before they spread. Customers get a detailed breakdown of what needs attention now, what can wait, and what to monitor.
Customized Repair Plans Based on Building Type
Rubber roof repair plans are tailored to how each facility operates. A warehouse may need added protection at loading zones, while a retail space might need better drainage near HVAC units. At Miller’s Commercial Roofing, we consider use patterns, foot traffic, equipment placement, and weather exposure when designing repair strategies. This helps extend the life of the roof without spending on unnecessary work.
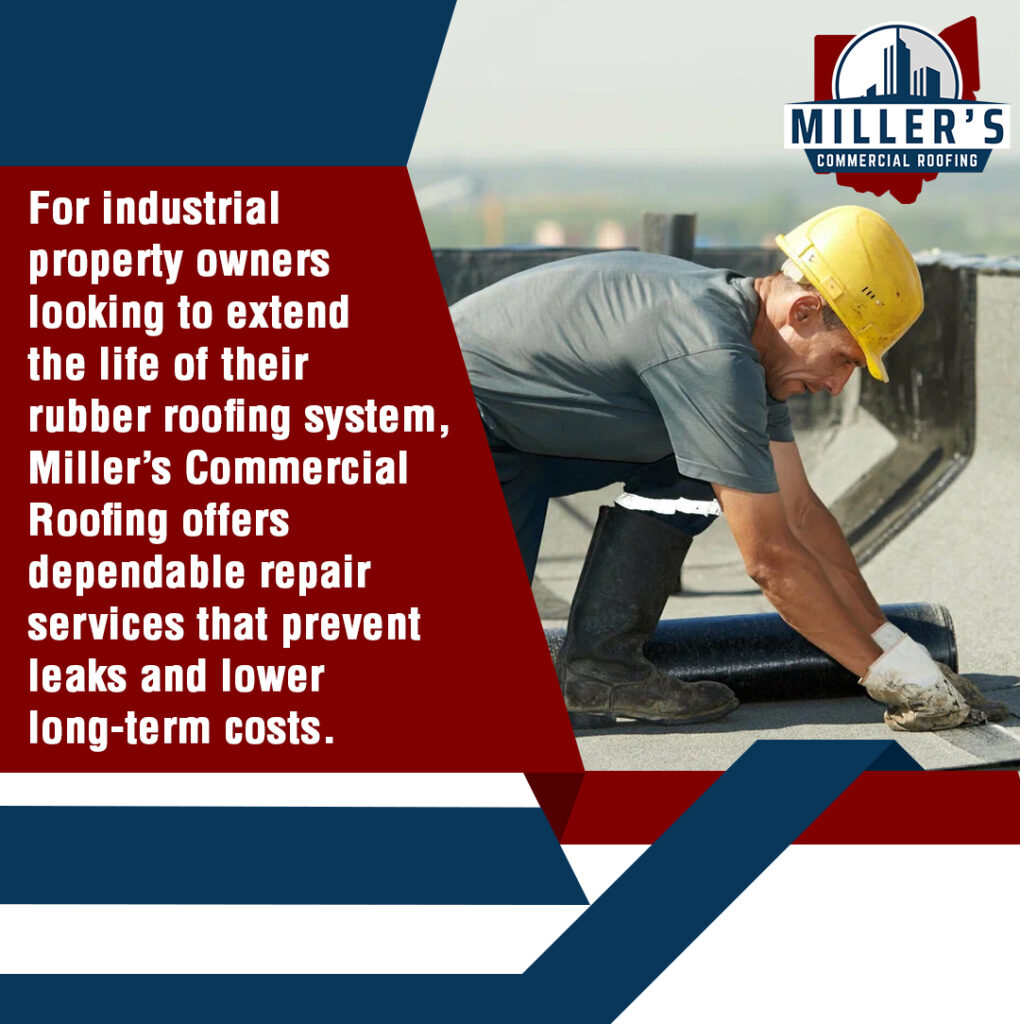
Long-Term Partnerships with Local Businesses
Miller’s Commercial Roofing builds working relationships, not just repair schedules. Many customers in Canal Fulton return for future repairs, coatings, or upgrades. We offer scheduled checkups, preventative maintenance options, and repair tracking to help clients stay ahead of problems. This consistency helps keep buildings dry, safe, and more energy-efficient year after year.
Protecting Your Rubber Roof Investment in Canal Fulton
Regular repairs and inspections can add years to the life of a rubber roof. For industrial properties in Canal Fulton, OH, ignoring minor issues can lead to costly water damage, higher energy bills, and safety risks. Working with an experienced commercial roof repair contractor like Miller’s Commercial Roofing gives building owners access to practical repair plans, honest guidance, and local service.
Don’t wait for small issues to become costly problems. Contact Miller’s Commercial Roofing today for expert rubber roof repairs and maintenance. Our team offers tailored commercial roof repair services for businesses in Canal Fulton, OH. Call us at (330) 491-6087 or email peter@millerscommercialroofing.com to schedule your roof evaluation and get started!